Es ist kaum zu glauben, aber es gibt Situationen auf Baustellen, die beanspruchen unsere Messgeräte bis an ihre Grenzen und auch darüber hinaus. Dazu zählen z.B. Angriffe von Baggern, Verschüttung mit Sand, Schwimmkurse oder Feuer.
Um unsere Messgeräte bestmöglich auf alle Formen von Alltagsstress vorzubereiten, machen wir auch immer wieder Tests und Prüfungen in Haselünne.
Es folgen ein paar Beispiele aus dem Alltag auf der Baustelle und wir gewähren Ihnen Einblicke in die internen Verfahren im Hause Esders.
Warnhinweis: Sollte es Ihnen an Humor mangeln, lesen Sie ab hier bitte nicht weiter.
OLLI
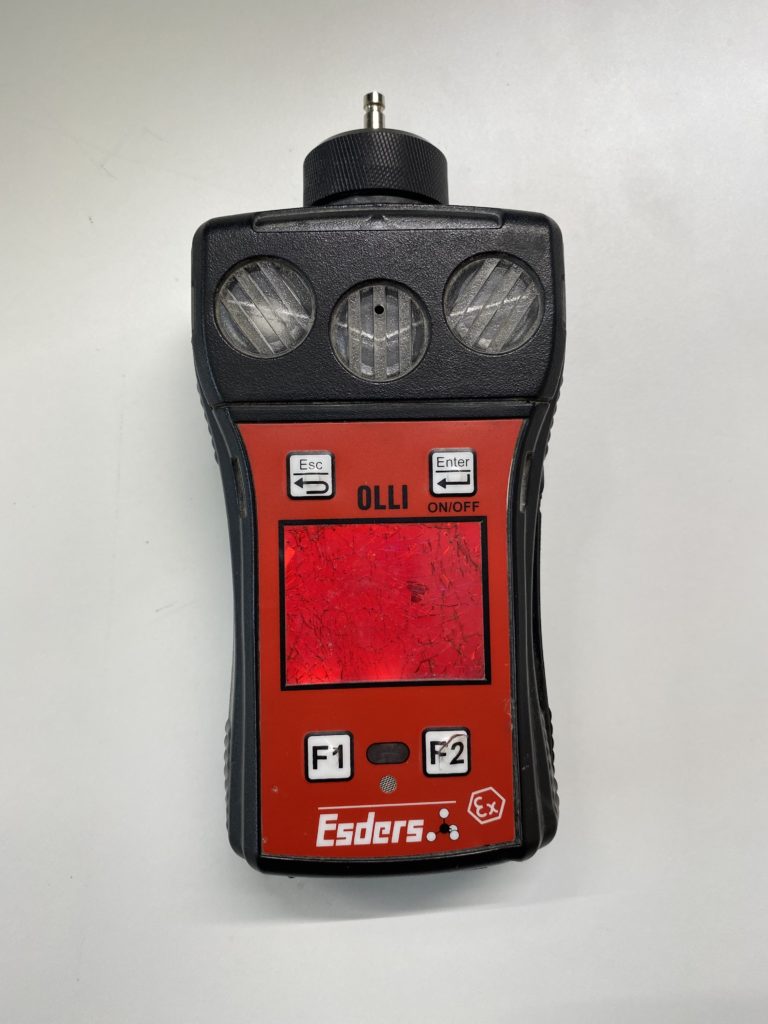
Unser wunderschönes OLLI wurde auf relativ weichem Untergrund von einem Bagger überfahren. Einschalten kann man es noch und der Alarm funktioniert auch, aber sicheres Arbeiten ist mit diesem Messgerät definitiv nicht mehr möglich, da das Gehäuse Risse aufweist. Das Display überzeugt auch nicht mehr.
DruckTest GaWa
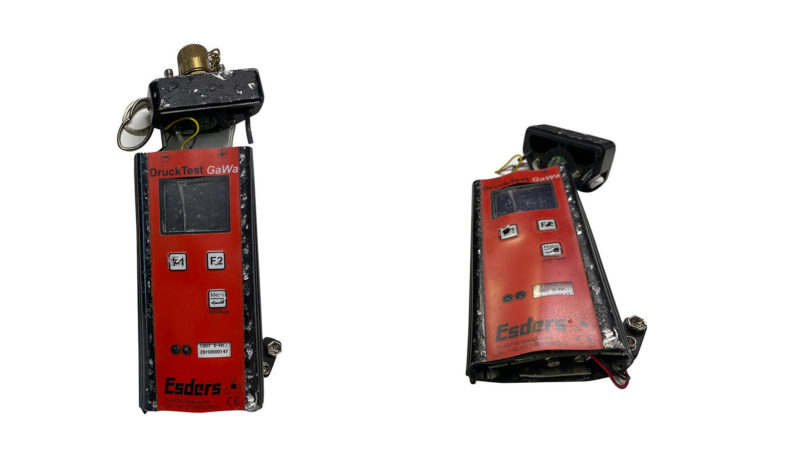
Als weiteres Highlight präsentieren wir das DruckTest GaWa „Slimline“ auch hier kam ein Bagger zum Einsatz. Das Aluminiumgehäuse hat nachgegeben, aber der eingebaute Sensor ist noch gut erhalten, da die Sensoraufnahme aus dem Vollen gefräst wird.
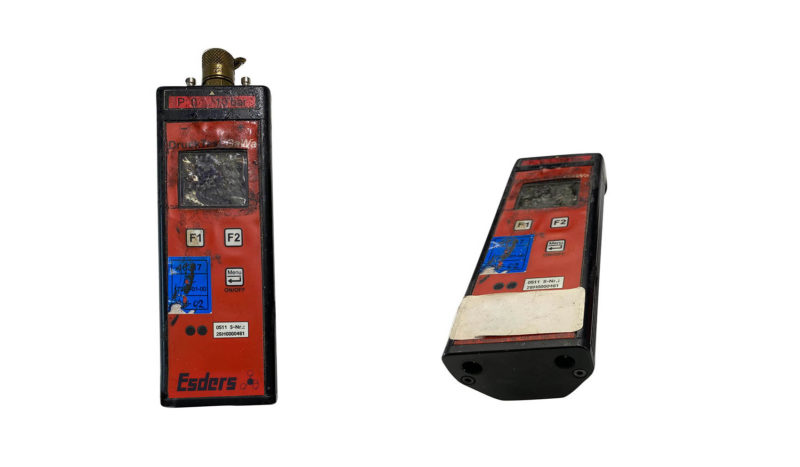
Neben dem Bagger ist offenes Feuer ein natürlicher Feind unserer Messgeräte. Das hier zu sehende DruckTest GaWa lag in einem Auto, dass ausgebrannt ist. Wie es dazu kommen konnte, weiß angeblich keiner mehr. Wir bitten doch sehr den Temperatureinsatzbereich der Geräte einzuhalten. 😂
DruckTest memo
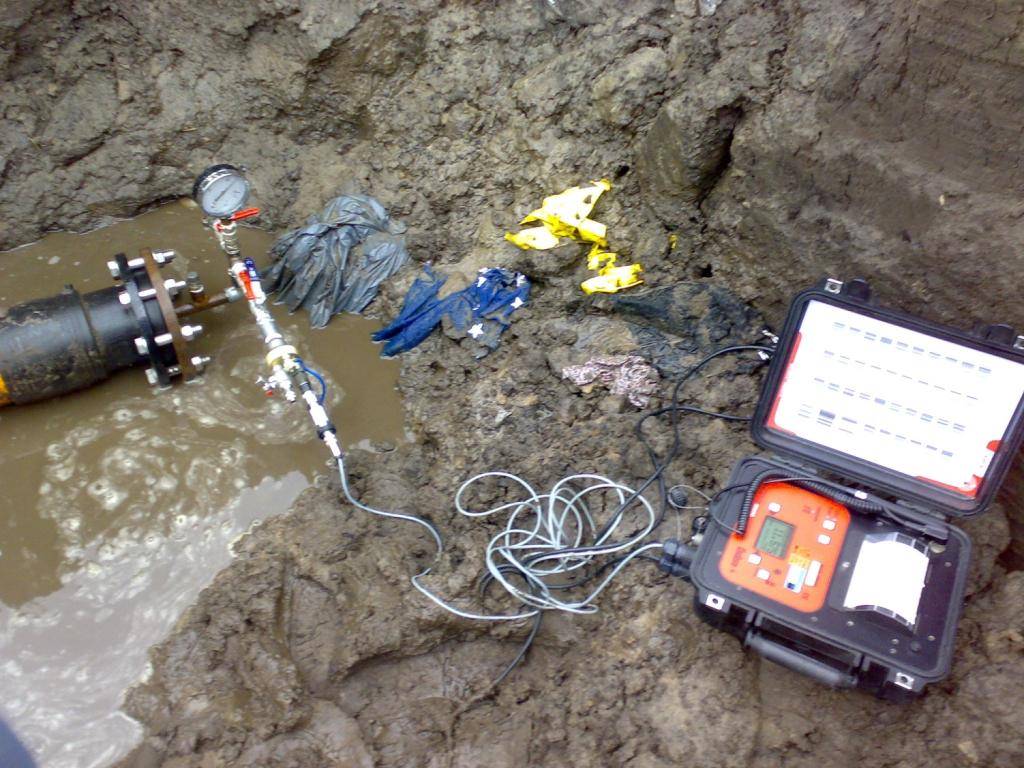
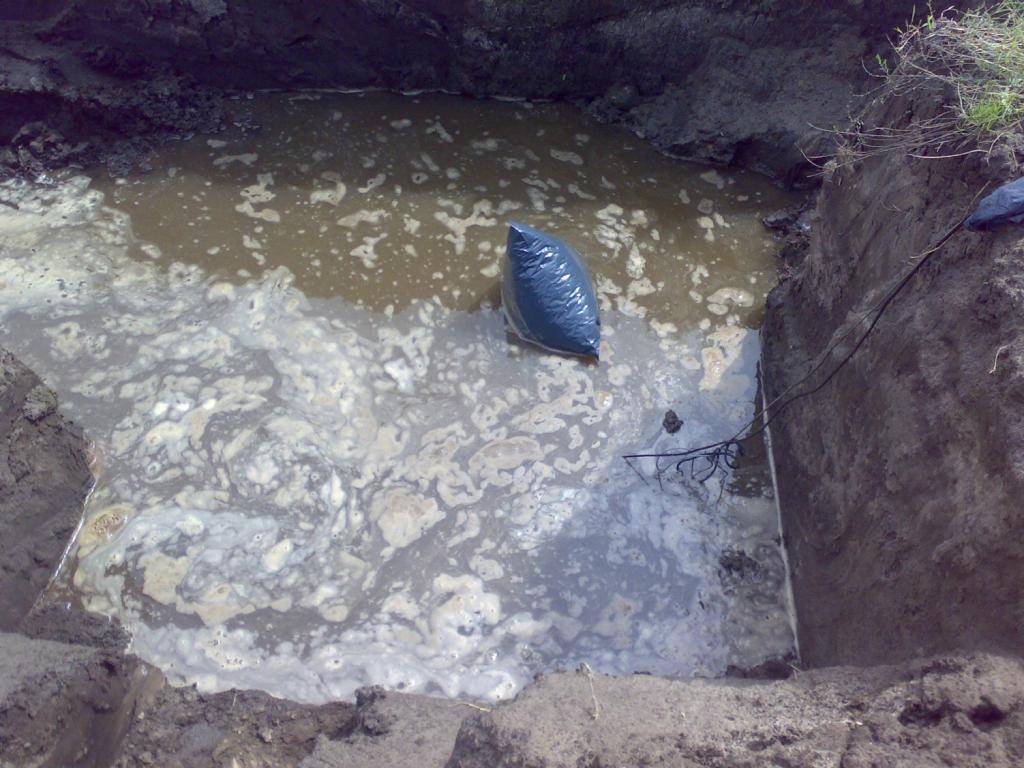
Nicht ganz ordentlich abgesicherte Baugruben stellen manchmal die höchsten Anforderungen an unsere Geräte. Nach der erfolgreich bestandenen Prüfung zum Seepferdchen (einschließlich Tauchgang), melden wir das DruckTest memo jetzt für das Bronze Abzeichen an.
Tests für die harte Praxis - Bitte nicht nachmachen!
Einige Tests führen wir in Haselünne auch mit großer Freude selbst durch, wie z.B. der Fenstersturz unseres OLLI in der Entwicklungsphase. Dabei stellten wir fest, dass die Platinenbefestigung an einer Position noch nicht optimal ist.
In der Flugphase sehr elegant, durch den Aufprall leiden Gehäuse und Sensoren allerdings sehr.
Diese internen Prüfungen reichten uns 2019 allerdings nicht mehr aus und wir haben daraufhin ein hochqualifiziertes Experten-Team zusammengestellt. Unsere Experten haben im Labor verschiedene Experimente unter extremen Bedingungen durchgeführt.
Und falls Sie das noch nicht gesehen haben, hier die Aufnahmen aus unserem Test-Labor.
Aber Scherz beiseite – wie wir bei Esders unsere Produkte wirklich testen
Für neue Produkte gibt es einen genau vorgeschriebenen Ablauf von der Entwicklung hin bis zur Auslieferung und darüber hinaus.
Neue Produkt-Anforderungen kommen in der Regel aus dem Marketing, Vertrieb oder der Geschäftsführung und werden durch das Produktmanagement gesammelt und dann im Detail mit der Entwicklungsabteilung besprochen.
Daraufhin werden im nächsten Schritt erste technische Dokumente erstellt und Prototypen entwickelt. Hier ist ein ATEX-Experte als Hardware-Entwickler bereits involviert. Nicht alle unsere Produkte benötigen eine Zertifizierung im Bereich Explosionsschutz.
Bei einem neuen Gehäuse ist das Handling sehr wichtig. Während wir früher mit Holzmodellen oder sogar Lego versucht haben neue Gehäuse zu bauen, kann jetzt ein Gehäuse aus dem 3D-Drucker helfen, das Handling zu testen und ggf. Optimierungen durchzuführen.
Prototyp OLLI
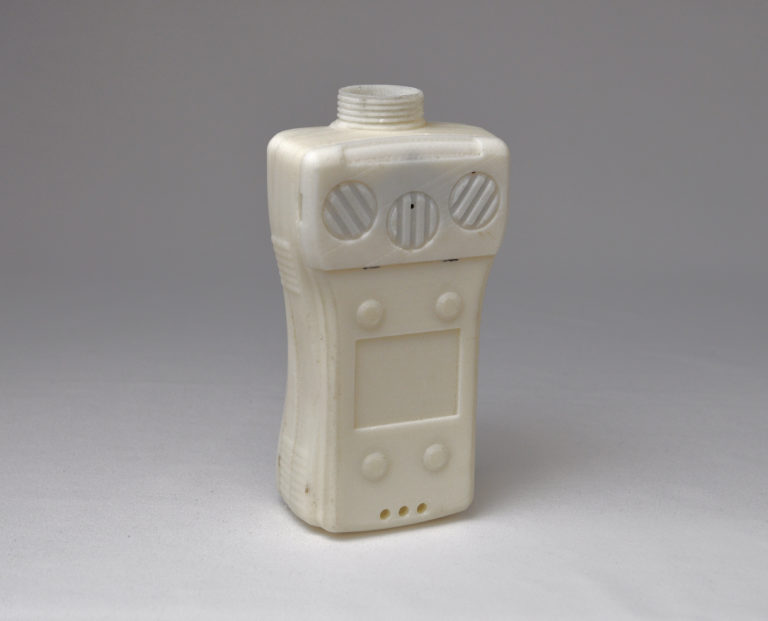
Erste Prototypen werden aufgebaut und getestet. Hierbei sind die Qualitätssicherung (QS) und die Entwicklung beteiligt. Wenn in einem Produkt neue Sensoren verbaut werden sollen, die hier im Hause noch nicht verwendet wurden, dann werden diese vor ihrer Verwendung an unterschiedlichen Umweltbedingen (Temperatur, Luftfeuchtigkeit, Luftdruck, Gaskonzentrationen) geprüft.
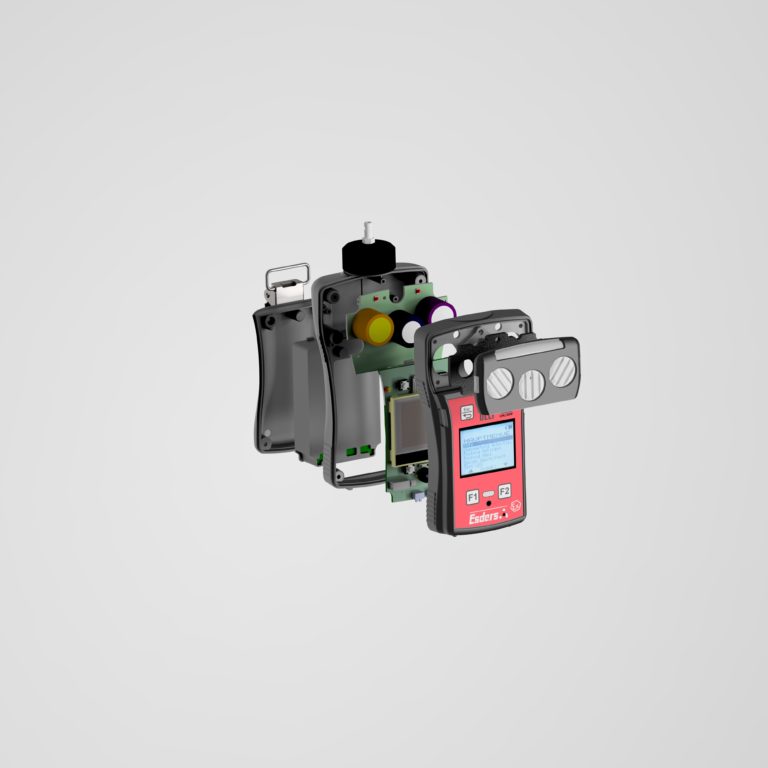
Funktionstests und Baustellentauglichkeit
Wir führen einen allgemeinen Funktionstest durch und verschiedene Funktionstests bei unterschiedlichen Temperaturen in unserem Klimaschrank.
Dann wird die Messgenauigkeit bei unterschiedlichen Umweltbedingungen geprüft (hohe & niedrige Temperaturen, verschiedene Luftfeuchtigkeit, unterschiedlicher Umgebungsdruck im Klimaschrank oder anderen Vorrichtungen).
Es erfolgt eine Kontrolle der Stromaufnahme in den verschiedenen Menüpunkten und wir testen die Akkus und die Ladetechnik.
Danach führen die Produktion und unser Service einen Test der automatischen Justage & Kalibrierung durch und einen Test der Kundenjustage.
In einem nächsten Schritt prüfen wir die Datenübertragung zu einer PC Software oder in die Cloud (wenn vorhanden).
Außerdem wird geprüft ob die Geräte wasserdicht sind und es wird ein Falltest zur Prüfung des Gehäuses auf „Baustellentauglichkeit“ durchgeführt.
Dokumentation, technische Zeichnungen, Schaltpläne
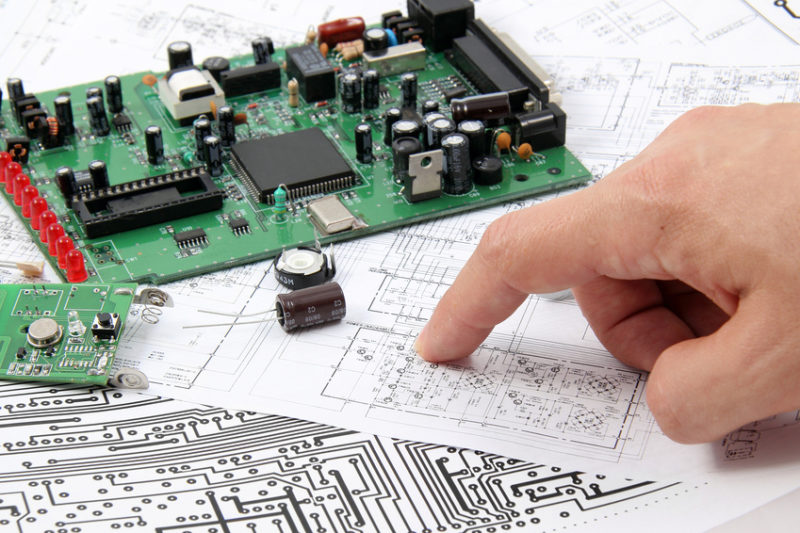
Umfangreiche Dokumentationen, technische Zeichnungen, elektrische Schaltpläne und weitere Dokumente für das Messgerät werden für die externe Prüfstelle erstellt.
Die sogenannte „Null-Serie“ wird unter Einweisung der beteiligten Entwickler und durch zur Verfügungsstellung der notwendigen technischen Dokumente von der Produktion gefertigt.
Durch die Erfahrungen beim Bau der ersten Null-Serie werden „Montageanleitungen“ erstellt. Es wird detailliert festgelegt, wie ein Produkt zu bauen ist. Dies wird dann durch den ATEX-Beauftragten geprüft und freigegeben und es werden parallel QS-Prüfungen in der Produktion installiert.
Die Null-Serie wird nochmals durch die QS-Entwicklung (Funktions- & Sicherheitsaspekte) sowie durch das Produktmanagement und den Vertrieb (Kunden-Anforderungen) auf Herz und Nieren geprüft.
Parallel dazu werden schon sogenannte „Baumuster“ erstellt und zu einem externen Prüflabor gesendet und dort getestet.
Nach erfolgreichen externen Tests wird die EU-Baumusterprüfbescheinigung durch das externe Prüflabor ausgestellt.
Alle weiteren sicherheitstechnischen Veränderungen am Produkt müssen ab jetzt, jeweils über Nachträge zur ausgestellten EU-Baumusterprüfbescheinigung, von der externen Prüfstelle genehmigt werden.
Wenn alles zufriedenstellend ist, wird die Serienproduktion aufgenommen.
In der laufenden Serienproduktion bleibt der Fertigungsablauf gleich und die Qualität wird durch die QS-Fertigung überwacht. Wenn Änderungen notwendig sind, können diese immer nur nach Prüfung durch den ATEX-Beauftragten durchgeführt werden. Dieser prüft auch ob eventuell ein Nachtrag für die EU-Baumusterprüfbescheinigung erforderlich ist.
Unsere Qualitätssicherung endet nicht mit der Auslieferung des Gerätes!
Sehr viele Geräte kommen zu einer jährlichen Wartung zu unserem Service wieder zu uns ins Werk oder werden auf dem Mobilen Service von uns regelmäßig überprüft. Zusätzlich nehmen wir jede negative Kundenrückmeldung durch den technischen Support als Reklamationen in unser ERP-System auf. Damit haben wir eine sehr gute Datenbasis, um die Qualität unserer Geräte über den gesamten Produktlebenszyklus beurteilen zu können.
Wir wissen also ziemlich gut, welche Bauteile, Funktionen, etc. nach vielen Jahren im Betrieb noch gut funktionieren und welche nicht mehr so gut sind und reagieren auch entsprechend darauf.
Es ist ein langer Weg von der Idee bis zum Produkt. Aber nur so können wir die Anforderungen unserer Kunden aufnehmen und qualitativ hochwertig umsetzen. Und wir wollen weiter analysieren und die Prozesse verbessern.
Damit das auch für eine steigende Anzahl von Produkten funktioniert, haben wir die Entwicklung auf ein Team von mittlerweile 20 Personen verstärkt.
Wir arbeiten mit großer Freude an neuen Lösungen – für Sie.